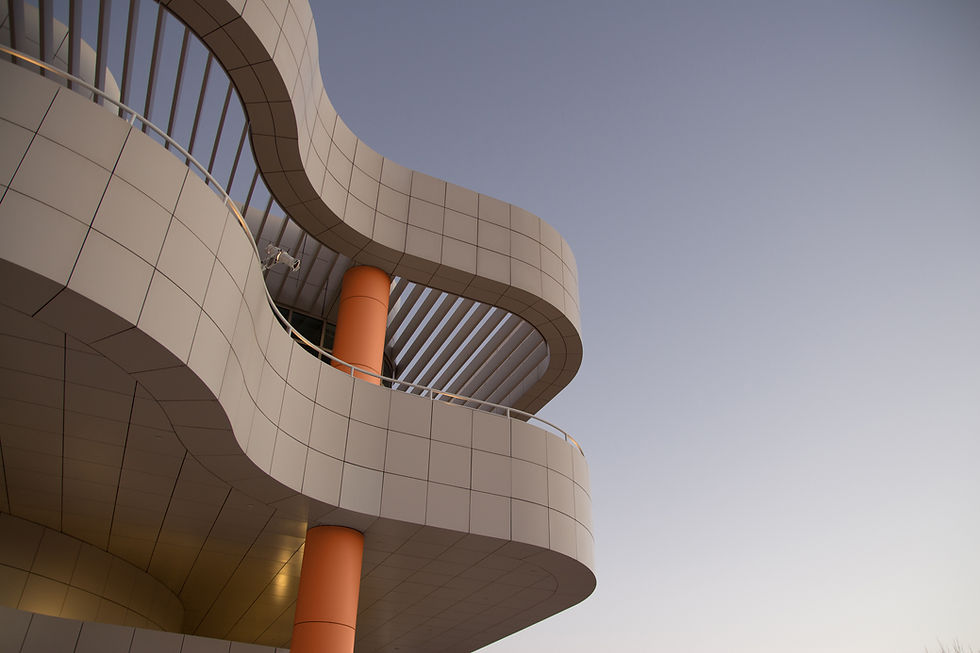
Quality Function Deployment (QFD): Translating Customer Needs into High-Quality SolutionsBy Northern Institute for Industrial Six Sigma (NIISS)
Oct 16, 2024
2 min read
0
0
0

In today’s competitive landscape, understanding and addressing customer needs is essential for business success. The Northern Institute for Industrial Six Sigma (NIISS), an accredited body by the Council for Six Sigma Certification, empowers professionals with tools like Quality Function Deployment (QFD) to transform customer insights into actionable project goals and deliver exceptional value.
What is Quality Function Deployment (QFD)?
QFD is a structured methodology used in Lean Six Sigma to capture customer requirements and integrate them into the design and development of products or services. Often referred to as the Voice of the Customer (VOC) translation tool, QFD ensures that every process aligns with customer expectations, enabling businesses to deliver high-quality, customer-focused solutions.
Key Components of QFD
Voice of the Customer (VOC):Identify and prioritize customer needs through surveys, interviews, and feedback. VOC serves as the foundation for QFD.
House of Quality (HOQ):A visual tool central to QFD, the HOQ translates VOC into technical requirements, ensuring alignment with customer priorities.
Prioritization Matrices:Use matrices to rank customer needs and align resources with the most impactful areas.
Interdepartmental Collaboration:Foster collaboration across teams—marketing, design, production, and quality—to ensure seamless integration of customer feedback into project goals.
How QFD Works in Lean Six Sigma
Define Customer Needs:Begin with thorough VOC analysis to identify explicit and implicit customer requirements.
Translate Needs into Goals:Use the HOQ to convert customer needs into measurable technical specifications.
Design and Develop Solutions:Develop product or service designs based on technical requirements while considering feasibility and cost-effectiveness.
Validate Results:Test prototypes or solutions to ensure they meet or exceed customer expectations.
Continuous Improvement:Incorporate feedback loops to refine processes and enhance product or service quality continually.
Benefits of QFD
Enhanced Customer Satisfaction:Deliver solutions that directly address customer needs and expectations.
Reduced Development Time:Avoid costly design iterations by integrating customer feedback early in the process.
Improved Resource Allocation:Focus efforts on high-priority areas that have the greatest impact on customer satisfaction.
Stronger Cross-Functional Collaboration:Break down silos by fostering communication and teamwork across departments.
Real-World Applications of QFD
Automotive Industry:Leading automakers use QFD to integrate customer preferences, like safety features and fuel efficiency, into vehicle designs.
Healthcare:Hospitals employ QFD to enhance patient care by aligning services with patient needs, such as shorter wait times and personalized treatment plans.
Software Development:QFD helps developers create user-friendly applications by incorporating customer feedback into design and functionality.
Why Choose NIISS for QFD Training?
At NIISS, we provide practical training on Quality Function Deployment, equipping professionals with the skills to:
Capture and analyze VOC effectively.
Develop HOQs tailored to business needs.
Align product development with Lean Six Sigma principles.
With Council for Six Sigma Certification accreditation, our programs are recognized globally, ensuring that you gain industry-relevant expertise to advance your career.
Take the First Step with NIISS
Join the thousands of professionals who have transformed their organizations through QFD and Lean Six Sigma methodologies. With a mission to empower 200,000 professionals by 2026, NIISS is your partner in driving operational excellence.
Ready to master QFD and deliver high-quality solutions?